24/7 Visibility Into Your Entire Medical Inventory
SQ.track™ Instrument Tracking Software powered by Ascendco Health helps to eliminate inefficiencies, assist in compliance and gain full control of your surgical instrument inventory.
Can you trust your tracking data to keep you updated 24/7? Effectively managing SPD operations requires complete visibility into the movement of surgical sets throughout the reprocessing lifecycle.
53% of OR delays come from inefficient processes and inventory tracking.1 Hospitals looking to grow their surgical operations cannot afford for their surgical asset management to be guided by incomplete or unclear data.
If your hospital’s legacy system isn’t equipped to provide the efficiency and accuracy proper visibility requires, Aesculap can help.
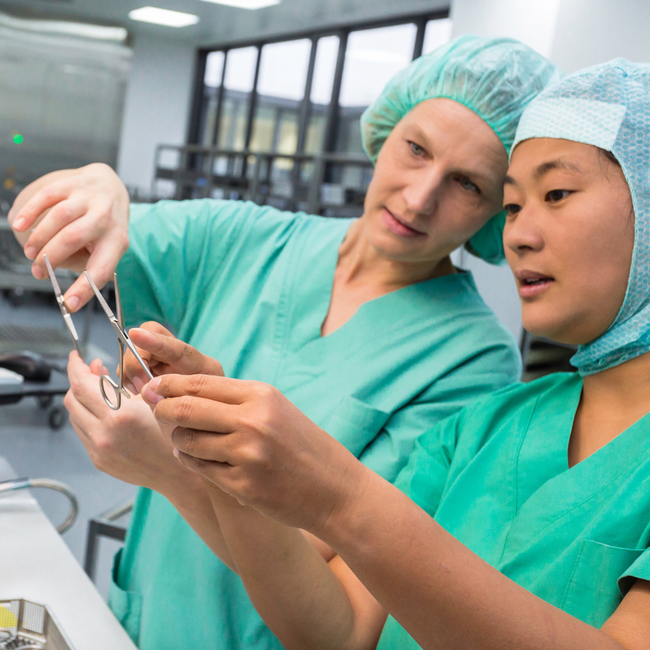
Visibility that puts you in control
SQ.track Instrument Tracking Software is a cloud-based surgical instrument tracking system that manages assets and processes to capture in-depth, usable data throughout the reprocessing cycle. With an industry-leading focus on accuracy, accessibility and ease of use, SQ.track Instrument Tracking Software simplifies the process for hospital staff to:
- Quickly locate instruments, reducing wait times and increasing SPD efficiency
- Assist in SPD compliance thanks to robust and easy-to-access tracking and analytics
- Upgrade current tracking with simple implementation supported by our expert team
The tools that enable actionable inventory insights
Real-time location tracking (RTLS)
Integrated RTLS solution tracks surgical set location with automation and analytics.
EMR compatibility
Inventory lists are pulled directly from EMR for fast, easy access to reprocessing data and nomenclature automation for elimination of dead records.
Multiple powerful modules
Customize your dashboard to fit your hospital’s exact needs with modules for back-stock or loaner modules that enforce vendor accountability.
Superior account management
Assist in SPD compliance with embedded analytics, event quality checks and data organization to establish department accountability through quality controls.
Ascendco cloud-based architecture
Scalable, low-maintenance technology that can fit seamlessly into existing hospital IT systems without needing additional hardware.
Contact us
Take control of your surgical assets
Ready to optimize your surgical assets? Connect with Aesculap to explore surgical asset management solutions that drive efficiency, compliance and growth for your facility. Contact us now and schedule a customized consultation.
Your request could not be submitted. Please try again.
warning1Aesculap Data on File